Standing tall amid a forest of CDMOs: Saying "no" to outsourcingStanding tall amid a forest of CDMOs: Saying "no" to outsourcing
Despite the growth of outsourcing and the enthusiasm surrounding it, an executive from GenVivo says that in-house manufacturing might remain a viable alternative for companies willing to go through the steps.
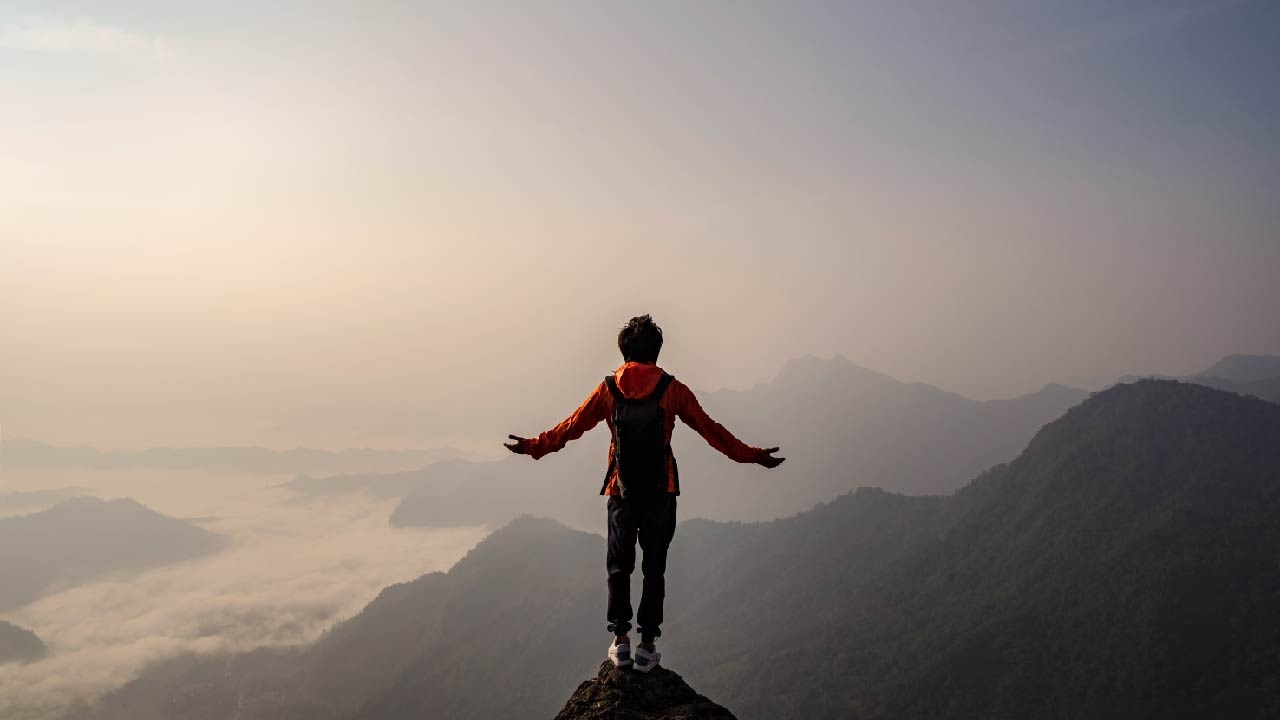
In his address at BioProcess International (BPI) West in San Diego, California, Victor Constantinescu, head of manufacturing and business development at startup biopharmaceutical firm GenVivo, said that with proper planning and the right investment, in-house manufacturing can be a viable and cost-effective option for drug developers, even as the influence of contract development and manufacturing organizations (CDMOs) continues to grow.
Constantinescu pointed out a few key advantages for in-house manufacturing: He said that it enables companies to maintain direct process control while giving them maximum protection of their intellectual property. It also allows for scheduling flexibility, since there is no need to compete with other drug developers for manufacturing slots.
Conversely, even with those advantages, some companies may not choose to manufacture in house due to potentially prohibitive high-capital investment, which can be over $100 million for a facility, plus equipment costs. Manufacturing also requires specialized expertise, requires a substantial time investment before new facilities can be rendered operational, and requires developers to take on all the risk without sharing the responsibility for production and regulatory compliance with a CDMO partner.
Blazing a trail
Constantinescu said the short and long-term decisions companies make regarding vector-based therapy manufacture are critical, especially when considering production complexity. He added that such decisions can have a big impact on clinical development timelines, costs, and ultimately the ability for patients to gain access to potentially life-saving therapies.
“We actually had originally started by using a CDMO when the company first began,” Constantinescu said about the early days of GenVivo. “And the issues began when they weren’t able to meet our investor and our board’s timelines.”
Shortly after, GenVivo decided to produce its own therapies. “There’s a very significant upfront cost to purchase all your equipment,” Constantinescu said of opening a GMP space. The company also needed to factor in overhead and the timeline it would take to get off the ground. Aside from the need to search and train employees, the team also needed tools. “Equipment lead times are not short,” he said.
But the advantages included more control of the manufacturing timeline and the ability to adjust manufacturing practices flexibly. “We were making adjustments to our manufacturing process very frequently to increase purity, potency, and consistency.” He emphasized the benefit of transitioning from R&D to manufacturing swiftly and on his company's own timeline.
As demand increased, the company discussed partnering with a CDMO. After speaking with several such companies, Constantinescu discovered that with increased production, his company could save money compared with its current costs. But with further research, the team realized that the company could save even more money by expanding into a larger facility and continuing to manufacture in house.
Rather than go with the lengthy and expensive permit and construction process required of building a new greenfield facility, the company leased a brownfield facility, thus avoiding significant upfront capital expenditure. From there, GenVivo selected a site, which meant considering location, size, power and zoning requirements, and the potential for expansion.
For companies looking to follow suit, Constantinescu recommended hiring a broker to deal with the complicated nature of choosing a site and a lawyer for the myriad legal complications that come with signing a deal and maintaining a new property. He said such agreements are hundreds of pages long and require a keen legal eye to square away.
And when it comes to converting a facility for GMP use, “there’ll be a full army of people helping out,” Constantinescu said. “More than you can imagine.”
To assemble the right team, he recommended starting with a construction project manager capable of defining the pace of the project. “They’ll help you select an architect, a general contractor, and engineers, vendors, consultants.”
Time and cost
“For a mid-size biotech facility, you’re probably thinking about two or three years,” Constantinescu said regarding the probable timeline. But he added that there is a lot of variability, with most of it in the longer direction.
And the cost of a new facility is similarly variable, estimated between $1000 and $2000 per square foot. “Where do you make cuts and compromises in a building?” To build top of the line modular cleanrooms, companies will end up at the higher end of that estimate, he said.
CDMOs are on the rise, and their impact on the biopharmaceutical industry is here to stay. But for companies with the time and resources to do it themselves, there remains a viable and potentially lucrative path forward.
About the Author
You May Also Like