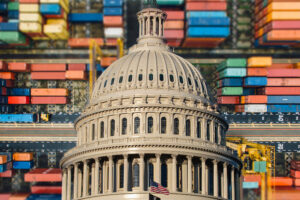
Manufacturing roundtable offers tips for businesses to stay abreast of tariffs, skilled worker shortage
By onBusiness Practices | Market Trends
A new report focused on manufacturing trends in the Pacific Northwest sheds light on some interesting manufacturer standpoints regarding inflation, supply chain issues, and skilled workforce shortages that collision repair facility owners could learn from to benefit their shops.
Schwabe, a group of manufacturing sector legal professionals, and Aldrich, manufacturing sector CPAs and advisors, implemented a survey of manufacturers during Q4 2024. The results are shared in its third “State of the Manufacturing in the Pacific Northwest.” The first survey was fielded in 2018 followed by another in 2021 amid the COVID-19 pandemic.
Carrie Sowders, Aldrich partner and manufacturing industry group leader, said during a virtual roundtable on Wednesday that three-quarters of the survey respondents are based in Oregon participants (heavily in the Portland Metro area), one quarter in Washington State, and 5% outside those general areas.
A pie chart in the report breaks down the types of manufacturing the respondents represent.
Mike Cohen, Schwabe shareholder and manufacturing industry group leader, noted the survey was conducted before the Trump Administration’s new policy changes within his first 60 days in office.
Since that was the case, and tariffs have been one of the biggest news items affecting manufacturers of late, Cohen polled roundtable participants Wednesday.
“Just as I suspected, tariffs are super high on everybody’s mind right now and the potential impact that those tariffs are going to have on supply chains,” he said. “At the time we originally put the survey into the field, only 67% of overall respondents identified supply chain as being a potential issue, and frankly, tariffs weren’t even on the radar at the time. Things have changed a little bit, but I do think as a general proposition, the idea of rising costs generally is still surfacing to the top.”
Jim Gaylord, Schwabe associate and business/corporate attorney, added that state laws and inflation were at the top of everyone’s minds rather than federal changes when the survey was conducted.
He noted since then, however, that there has been a flurry of implemented and impending tariffs.
“We have the 25% tariff on steel and aluminum imports, which has been in effect since mid-March, and then the additional 20% tax on Chinese imports, which has been in effect since early February,” Gaylord said. “Recently, we’ve seen a handful of new ones come into play — the tariff on imported automobiles, which went into effect today [Wednesday], and there’s a pending additional tariff on automobile parts, which should come into play in early May.
“I’m sure a lot of you have been watching the back and forth with the tariffs on Mexican and Canadian goods… Those tariffs are set to come back into play today [Wednesday] and the Senate is currently voting on a resolution to block, at least, the Canadian tariffs to take effect.”
In addition, broad-sweeping tariffs were implemented Wednesday on any countries that have tariffs on U.S. goods, and fall somewhere between 10-20%, Gaylord added.
“Canada has a plan on imposing additional reciprocal tariffs on equipment and machinery,” Gaylord said. “Many Asian countries, in particular Japan, China, and South Korea, have announced that they will be working on a joint partnership in response to this situation and there will likely be a decreased demand on U.S. goods with a lot of these countries working more closely together. We anticipate that there might be a similar response in other areas of the world.”
As of Thursday afternoon, the Associated Press reported a 10% tariff on nearly all countries and territories. Higher levies will be imposed on about 60 nations that the Trump administration says are the “worst” offenders, including China.
Trump says those alleged offenders protect their producers through “malicious” trade practices and tariffs.
“Those efforts include actions such as imposing value-added taxes on all goods, dumping overproduced products on markets to artificially deflate prices, or manipulating currency,” the AP article states.
The 10% global tariffs take effect Saturday. The higher tariffs set for specific countries will begin April 9.
Gaylord provided some tips for businesses to respond to how tariffs could affect operations:
-
- Assess your situation and how you might be impacted: Analyze current contracts to see what pricing terms look like. Are prices fixed or variable based on changes in international tax policies, or anything else? Are there delivery terms that could be impacted?
- Look at your supply chain, in particular, if you have an inventory management system: Can it adjust to changing needs and demand-supply? Ensure the capability to make adjustments as necessary.
- Look at your overall cost structures and profitability
- Address internal structures to mitigate some changes, such as diversifying sourcing, or pulling some purchases forward to build up inventory now.
- Renegotiate contract terms to add fixed price clauses to help decrease market volatility impacts
- Raise prices to mitigate some of the extra costs.
- Stay aware of the ongoing situation.
One of the top three issues manufacturers said they face is attracting and retaining skilled workers, similar to the ongoing shortage of collision repair, automotive, and diesel technicians.
Jean Back, Schwabe shareholder and employment/labor attorney, said the problem continually comes to the top of the list in these surveys, and hasn’t changed a lot since the first in 2018.
“It’s a multifactorial approach when you’re looking at attracting a skilled workforce — you’re wanting a good work environment, obviously, someplace that people want to come to work every day,” she said. “Competitive wages are something that people are wanting. There are employees that will jump from one job to another for a dollar an hour more, and that was something that we saw a lot during the pandemic.
“Good leadership is a huge factor in keeping a good workforce. I think if people feel that the leadership from the top understands their concerns, understands what they’re doing, and is responsive — those are all things that can help to retain employees and attract a good workforce. And having said that, leaders should at least be on the floor occasionally so that people can see them… talking to employees, being personable, knowing people’s names. Those are all part of essentially making people feel like they’re part of your company and they’re seen and they’re heard. It does go a long way to making people want to stay and developing a feeling of loyalty to your company.”
Back added that flexible scheduling plus any assistance employers can provide for work and life quality improvement are always positive for employee attraction and retention.
Upskilling can also address workforce shortages, she said.
“If you have employees that are not necessarily skilled, but they’re doing more of the general labor type stuff, you can scale those employees up… to be able to do those jobs that you really need,” Back said.
Images
Featured image credit: Douglas Rissing/iStock
Charts provided during virtual roundtable presentation and/or within Schwabe and Aldrich’s “State of the Manufacturing in the Pacific Northwest” report.